Stephen Murphy & Emma Wills - Nelson - Tasman
How Tasman contract milkers solved their Thermoduric problem
Stephen Murphy started his contract milking journey in the Tasman region three seasons ago. They’ve been milking 500 cows through a large herringbone, which until recently, wasn’t running a wash through the plant as effectively as it should.
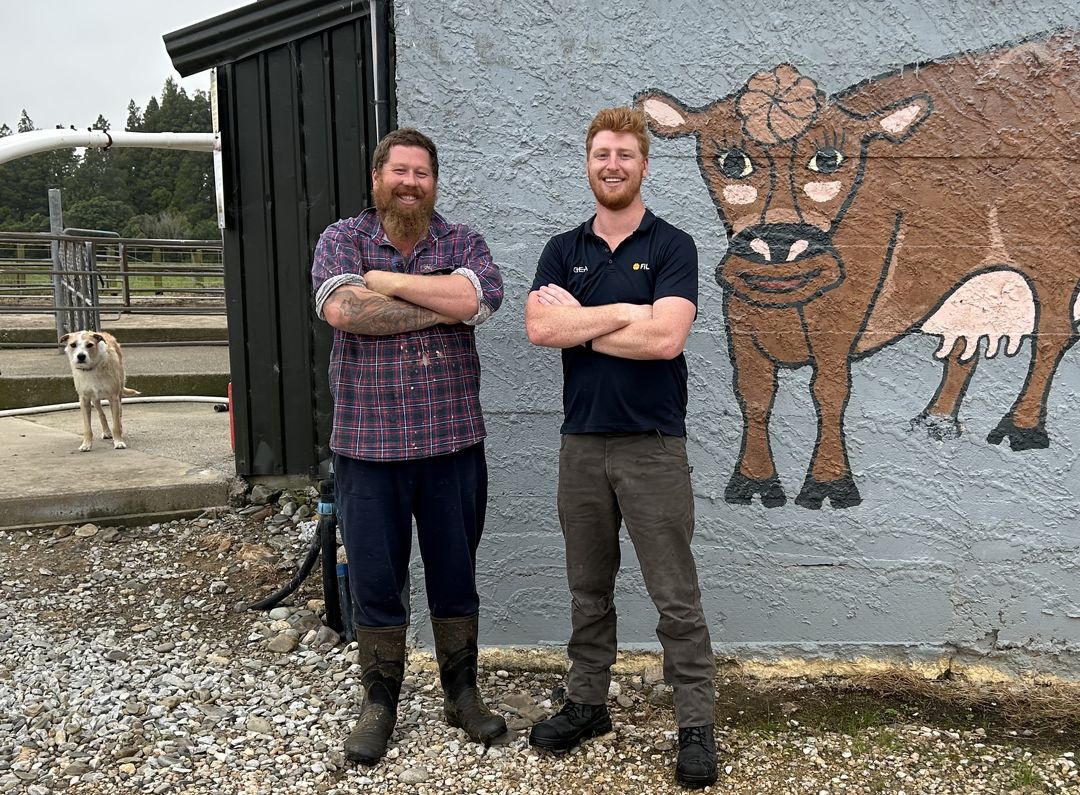
As a result, they were met with a Thermoduric problem that persisted for over a year. “It would come and go and cause us to grade occasionally. It was frustrating not knowing what was causing the problem,” Stephen said.
The couple had been using FIL since the beginning, but it wasn’t until their new FIL Area Manager, Ben Oxley, called in to introduce himself that they asked for help. Determined to help, Ben rolled up his sleeves and got to work.
“We had been using FIL products like Quantum Red, Quantum Powder, and C3 because I’ve always trusted their quality,” Stephen said. “But what really stood out was the level of support we received from Ben.
“Ben helped troubleshoot the issue with us, bringing tools like a milk line camera to find where the alerts were coming from.”
The camera revealed buildup in the milk line, a common area for fat and protein buildup, which was causing the Thermoduric alerts. Thermoduric bacteria (Thermo means heat and duric means to endure) are heat resistant and thrive in warmer temperatures. When hygiene related, the cause will be found somewhere in the milking plant.
Together, Stephen and Ben worked backwards to find the cause of the hygiene issue. They discovered that their old wash system wasn’t distributing water and detergent correctly. “It just wasn’t cleaning well enough, so we replaced the wash tub,” Stephen said. “Ben also ensured our chemical use rates were updated to ensure the plant was getting the correct amount of product.”
Now into their fourth season, the wash is going through the plant properly and the Thermoduric alerts have ultimately stopped. The improvements have brought significant peace of mind to the couple, knowing the quality of their milk is consistently good.
“The service we’ve received from Ben has been amazing. He has always been available to offer advice and support and ensure everything is running as it should. The time and effort Ben has put in is something you just don’t get anywhere else,” Stephen concluded.